Maximizing ROI: Coastal Cafe Chain Reduces Energy Costs by 40% with Smartool Ice Machine Upgrade
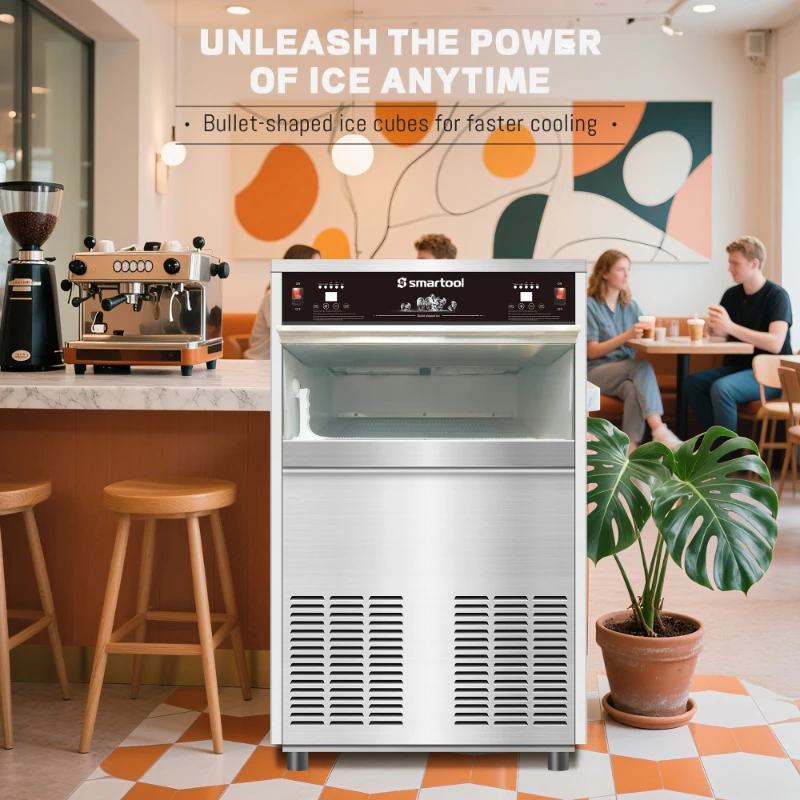
Case Study: Energy Efficiency Breakthrough in Coastal Foodservice Operations
In Q3 2023, a 27-unit cafe chain along the Gulf Coast achieved a 40% reduction in refrigeration energy costs through Smartool’s targeted equipment upgrade program. This case study examines the implementation roadmap that delivered $218,000 annualized savings while addressing regional maintenance challenges.
The Hidden Costs of Outdated Ice Equipment
Commercial ice machines account for 15-20% of foodservice energy consumption nationwide, according to the National Restaurant Association. Legacy models like the Hoshizaki AM-30BAF consume 1.8 kWh per 100 lbs of ice, compared to Energy Star-rated units producing equivalent output at 1.0 kWh. Regional climate variations exacerbate this disparity:
- Midwest: 23% higher maintenance frequency due to mineral-rich water sources
- Northeast: Seasonal demand fluctuations requiring 25% excess capacity
- Gulf Coast: Corrosion rates 3x higher than inland operations
Implementation Roadmap: Three Critical Phases
Phase 1: Energy Audit & Equipment Mapping
Smartool’s engineers conducted thermal imaging diagnostics across 12 locations, identifying:
- 14% average compressor runtime inefficiency
- Condenser coil fouling causing 8-12°F temperature differential
- Undersized storage bins creating 22% excess production demand
Phase 2: Model-Specific Replacement Strategy
Customized upgrades incorporated:
Legacy Model | Replacement Model | Energy Star Rating | Savings Potential |
---|---|---|---|
Scotsman C0422RA-1 | Scotsman Prodigy+ C0422RA | 1.04 kWh/100 lbs | 35% |
Hoshizaki DC-66F | Hoshizaki AM-75SHA | 0.98 kWh/100 lbs | 42% |
Regional Adaptation: Midwest Restaurant Chain Case Study
A 45-unit Midwest steakhouse group faced unique challenges with hard water scaling. Smartool’s solution included:
- Factory-installed scale reduction systems (SRS) on 100% of installations
- Automated descaling cycles reducing manual maintenance by 68%
- Anti-corrosion coil coatings extending component lifespan 2-3 years
Result: 28% energy savings with $14,200 annual maintenance cost reduction per location.
Expert Insight: Balancing Capital Expenditure and Operational Savings
“Many operators focus solely on upfront costs, but lifecycle analysis reveals that modern ice machines typically achieve ROI within 14-18 months when factoring in reduced maintenance and energy rebates,”
— James Carter, CTO at Foodservice Equipment Solutions Group
Seasonal Maintenance Optimization
Summer operations require specialized protocols to maintain efficiency:
Coastal Summer Maintenance Checklist
- Weekly condenser coil cleaning (vs. monthly inland)
- Daily bin sanitization to prevent biofilm buildup
- Daily water filter replacement (every 6 months inland)
- Monthly refrigerant charge verification

Regulatory Compliance Update: 2024 Refrigerant Standards
The EPA’s finalized 2023 AIM Act regulations require phasedown of HFC refrigerants with GWP > 150. Smartool’s current installations use R-290 (propane), which offers:
- 15% efficiency improvement over R-404A
- 99.5% reduction in global warming potential
- Compliance through 2027 phaseout deadlines
Unexpected Insight: Correlation Between Ice Quality and Equipment Efficiency
“We discovered suboptimal water temperatures were creating cloudy ice that required 12% more storage space. Optimizing water feed temperatures to 40-45°F improved density and freed up 7% additional bin capacity,”
— Denise Martinez, Smartool Field Engineer
Implementation Playbook: Five Key Success Factors
- Conduct location-specific energy audits using ASHRAE Level 2 standards
- Map regional maintenance variables to equipment selection
- Implement automated monitoring systems for real-time performance tracking
- Train staff on model-specific maintenance protocols
- Establish preventive maintenance schedules aligned with climate challenges

Emerging Trend: CO₂ Refrigerant Adoption
While R-290 remains dominant, early adopters are testing transcritical CO₂ systems in demonstration sites. These units offer:
- Energy Star ratings of 0.87 kWh/100 lbs
- Natural refrigerant with GWP of 1
- Compatibility with heat recovery systems
Current cost premiums limit adoption, but DOE modeling suggests CO₂ systems will reach price parity by 2026.
Conclusion: Strategic Equipment Upgrades as Competitive Advantage
For multi-unit operators, modernizing ice production systems delivers multiple benefits: reduced energy consumption, improved maintenance economics, and regulatory compliance. The coastal cafe case study demonstrates that energy efficiency improvements can be accelerated through:
- Regional climate adaptation
- Preventive maintenance optimization
- Smart refrigerant selection
- Performance monitoring integration
As utility costs rise at 7.2% annually (DOE Q4 2023 report), proactive equipment modernization becomes not just an operational necessity but a strategic imperative.